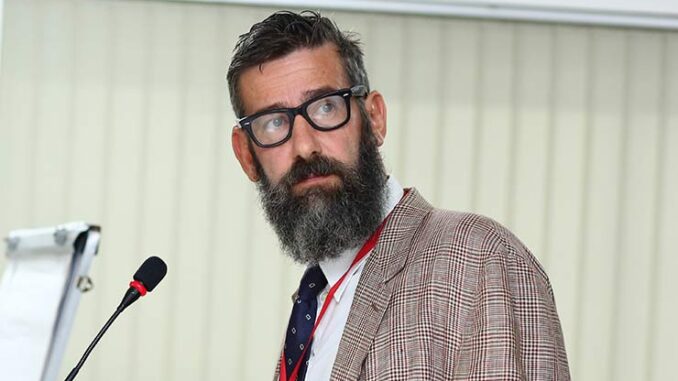
Comau offre ai propri clienti le tecnologie per la produzione e il montaggio di celle, moduli, pacchi batteria e powertrain elettrici destinati all’industria automobilistica e non solo. L’impegno nel settore dell’e-mobility è iniziato da circa 10 anni, come naturale evoluzione del core business e dell’impegno in ricerca e sviluppo che l’azienda porta avanti.
Fin dalla sua fondazione nel 1973 – l’azienda quest’anno compie 50 anni – Comau (COnsorzio MAcchine Utensili) sviluppa, costruisce e integra prodotti e sistemi di automazione per il settore automotive, in particolare per lo chassis delle auto. L’azienda opera a livello mondiale e si può stimare che oggi circa un quarto delle auto prodotte nel mondo abbia almeno una parte dello scheletro costruito con un impianto Comau. Oltre alla giunzione della scocca dei veicoli, anche il powertrain assembly, ovvero l’assemblaggio di motori e di cambi, rappresenta una competenza storica di Comau. A questo, si è affiancato il ramo delle macchine utensili per la lavorazione delle parti principali del motore endotermico (testa cilindri e corpo motore). Negli ultimi anni sono state emanate, in particolare a livello europeo, normative stringenti per la riduzione delle emissioni, per cui il comparto dedicato ai motori endotermici sta affrontando una progressiva trasformazione e riorganizzazione, volta a riqualificare le persone verso competenze legate all’e-mobility e, al contempo, supportare i clienti che richiedono ancora supporto per queste tecnologie.
Giancarlo Tronzano, responsabile delle tecnologie e-Mobility di Comau è tra i protagonisti di questo processo di crescita dell’azienda nel campo della mobilità elettrica. Tronzano gestisce un team di ingegneri sparso nel mondo e si occupa dello sviluppo di nuove tecnologie per i mezzi elettrici. Quindi celle, moduli, pacchi batteria, motori elettrici, trasmissioni. Nel prossimo futuro, il suo gruppo di lavoro inizierà anche uno studio sulle celle a combustibile a idrogeno, un’area di business su cui Comau è già attiva con importanti progetti e clienti in tutto il mondo.
La costruzione delle auto elettriche: cosa cambia per Comau
Il passaggio alla mobilità elettrica per Comau è stata un’evoluzione naturale ma anche una questione di sopravvivenza, visto l’orientamento del settore automotive verso i veicoli elettrici. Se, in precedenza, l’azienda creava linee di assemblaggio per propulsori tradizionali, adesso sviluppa sistemi di produzione per powertrain elettrici, costituiti da celle, pacco batteria, motore elettrico, riduttore e differenziale.
Per un cambiamento così importante l’azienda ha sfruttato gran parte delle competenze già presenti al suo interno, ne ha sviluppate di nuove e ha assunto personale esperto nel settore automotive elettrico. Comau ha avviato un importante programma di formazione interno, denominato e-Skill, che ha coinvolto oltre 1.000 dipendenti (su 3.700 totali) e contribuito a un’evoluzione del know-how aziendale. I progetti in ambito e-mobility stanno diventando la parte principale del business di Comau: negli ultimi anni la crescita è stata vertiginosa, con progetti sempre più grandi.
Parte delle tecnologie necessarie per i BEV (Battery Electric Vehicle) sono sviluppate all’interno, altre, più lontane dalle competenze dell’azienda, sono realizzate in collaborazione con partner e fornitori, integrate poi nei progetti Comau.
Oggi Comau fornisce linee di produzione complete dedicate alla costruzione di componenti per i veicoli elettrici. I componenti fabbricati dai sistemi dell’azienda sono i moduli che contengono le celle e i pacchi batteria che includono più moduli. I pacchi batteria sono poi assemblati nel frame, parte integrante dello chassis del veicolo. Comau sta facendo importanti investimenti per entrare nella produzione delle singole celle, un settore che offre importanti opportunità di sviluppo, dato che attualmente in Europa sono poche le aziende attive in questo campo.
L’azienda si occupa anche di linee sia per la costruzione dei rotori a magneti permanenti per i motori elettrici sia per l’assemblaggio finale della trasmissione elettrica (rotore, statore, ingranaggi di riduzione, differenziale).
Come Comau contribuisce alla produzione delle batterie
Oltre a sviluppare tecnologie innovative in ambito e-Mobility, l’azienda fa parte di diverse organizzazioni europee per stimolare la crescita di un sistema europeo di produzione delle batterie.
Da un punto di vista tecnologico, i sistemi di Comau si distinguono per velocità e flessibilità di produzione, caratteristiche molto importanti per i clienti. Per quanto riguarda le celle, le tipologie utilizzate oggi sono quelle cilindriche, prismatiche, pouch (a pacchetto), blade. Comau è impegnata prevalentemente in progetti per la costruzione di celle prismatiche e pouch.
In ottica di sviluppi futuri, l’azienda segue con attenzione l’evoluzione tecnologica delle batterie, in particolare di quelle a stato solido. Il Competence Center che Tronzano guida è impegnato anche nello sviluppo di processi di produzione di batterie diverse da quelle agli ioni di litio, come quelle basate sul sodio.
Per l’assemblaggio di più celle, la tendenza attuale è quella di semplificare la struttura del blocco batteria eliminando la fase di lavorazione intermedia, ovvero i moduli, che non danno alcun contributo energetico ma che incrementano il peso e i costi. L’obiettivo è arrivare a una produzione definita “cell to pack”. Questa semplificazione non è però indolore, perché aumenta la complessità del processo di assemblaggio: è necessario montare insieme molte decine di elementi (le singole celle), rispettando tolleranze e allineamenti. Per Comau è una sfida tecnologica importante, ma i vantaggi in termini di prestazioni e di costi sono significativi e giustificano ampiamente gli investimenti necessari per lo sviluppo del nuovo processo produttivo.
Le criticità nella costruzione delle batterie per auto elettriche
Le sfide che Comau affronta riguardano principalmente la rapidissima evoluzione del prodotto. Negli ultimi 10 anni il pacco batteria è stato rivoluzionato più volte. Capita che ci siano cambiamenti dei requisiti tecnologici anche durante lo sviluppo di un progetto.
Un altro elemento critico è dato dalla complessità sia del prodotto, che viene sviluppato attraverso il ricorso a diverse tecnologie, sia del processo produttivo, che deve massimizzare l’efficienza operativa in fase d’uso.
La scala dei progetti e la diversa tipologia della base dei clienti costituiscono altri punti che richiedono particolare attenzione. Comau deve gestire molti progetti in contemporanea, di grandi dimensioni e del valore di centinaia di milioni di euro, con tempi di realizzazione stretti. Per quel che concerne la base clienti, in passato Comau si confrontava con un numero limitato di costruttori di automobili, mentre adesso sono attivi sul mercato i cosiddetti ‘newcomers’, cioè produttori che si sono affermati negli ultimi anni, oltre a nuove aziende specializzate nella produzione di celle e batterie.
Dal punto di vista tecnico, il ‘time to market’ è un elemento fondamentale nelle strategie aziendali. Diventa quindi fondamentale per un’azienda come Comau riuscire a gestire le necessità che emergono in corso d’opera. Nonostante sia necessario un notevole sforzo, Comau è in grado di garantire questo tipo di supporto, come dimostrano numerosi progetti in corso che hanno richiesto un veloce passaggio dalla fase prototipale a quella produttiva.
Il contributo di Comau nello smaltimento e riciclo dei componenti di un’auto elettrica
Comau è impegnata nel campo dello smontaggio, riciclo e riuso, avendo già studiato tecnologie specifiche. Con un cliente europeo l’azienda ha cominciato a gestire un progetto relativo al riciclo degli scarti di produzione, che sono sempre presenti, anche nei processi più efficienti. Il progetto – di cui Comau segue alcune fasi – consiste nella realizzazione di una linea per preparare al riciclo le celle scartate, in modo da avviarle alla triturazione.
L’azienda sta sviluppando anche le tecnologie necessarie per il riciclo dei pacchi batteria. I pacchi devono essere smontati in sicurezza, perché le celle hanno di solito una carica residua. Questa attività non può essere svolta da persone – vista la pericolosità del processo – quindi deve essere demandata a macchine industriali, che in automatico aprono il pacco e smontano gli elementi interni, per avviarli alla fase successiva del processo.
L’obiettivo è quello di rendere il processo di smontaggio robotizzato sicuro e il più flessibile possibile, in modo da gestire pacchi batteria in diverse condizioni, ma anche di forma e costruzione differenti, sia pure entro certi limiti. Non è un’attività semplice: le tipologie di pacchi batteria sono centinaia poiché ogni produttore utilizza pacchi molto diversi. Il problema non è tanto meccanico quanto software: è necessario sviluppare un sistema di visione e di analisi che permetta il riconoscimento delle diverse tipologie di pacco e realizzare una libreria di processi facilmente utilizzabile dall’operatore.
Per quanto riguarda i motori elettrici, la tecnologia è matura da decine di anni e le attività di riciclo dei componenti sono gestite già da molti anni. La sfida, in questo caso, è quella di implementare processi capaci di trattare grandi volumi di pezzi da riciclare.